New Era in Electronic Components Manufacturing: Everything You Need to Know about SMD
In the ever-evolving landscape of modern electronics, the relentless pursuit of miniaturization, efficiency, and performance has given rise to surface mount devices. It is a revolutionary technology that has transformed the way we design, manufacture, and interact with electronic components. From the tiniest consumer gadgets to complex industrial machinery, SMD manufacturing has become an indispensable cornerstone of modern electronics.
In this article, we delve deep into the SMD world, shedding light on how the technology works and its advantages over through-hole counterparts.
Whether you are a seasoned electronics enthusiast, an aspiring engineer, or simply curious about the inner workings of some gadgets, this guide is your gateway to understanding the SMD assembly process from the ground up.
What is SMD technology?

Surface mount device (SMD) technology is a fundamental revolution in electronic components’ manufacturing. It has redefined the way elements are designed, manufactured, and integrated into a wide range of devices we use in our daily lives.
The essence of surface mount technology is that the components are mounted or placed directly onto the surface of the printed circuit boards (PCBs). Unlike traditional through-hole elements, SMDs are compact and lightweight, which have made them a dominant force in the electronics industry.
Surface mount technology VS. through hole:
In short, SMD components have a different physical construction and connection to the PCBs. Through-hole elements have wire leads that are inserted into the holes drilled into the PCB and then soldered on the other side. In contrast, SMDs have flat, thin metal leads or solder balls that sit directly on the surface of the printed circuit board, creating a more streamlined and space-saving design.
Even though the technologies are different, they can still be used on the same board. The reason is simple—not all components can be installed using the surface mount technology process (e.g., large transformers and heat-sinked power semiconductors).
However, SMD technology is considered revolutionary, as it made it possible to build highly complex electronic circuits into smaller assemblies with good repeatability. Thanks to the high level of automation, the development increases the maximum output and lowers the cost of production.
Advantages of Surface Mount Technology
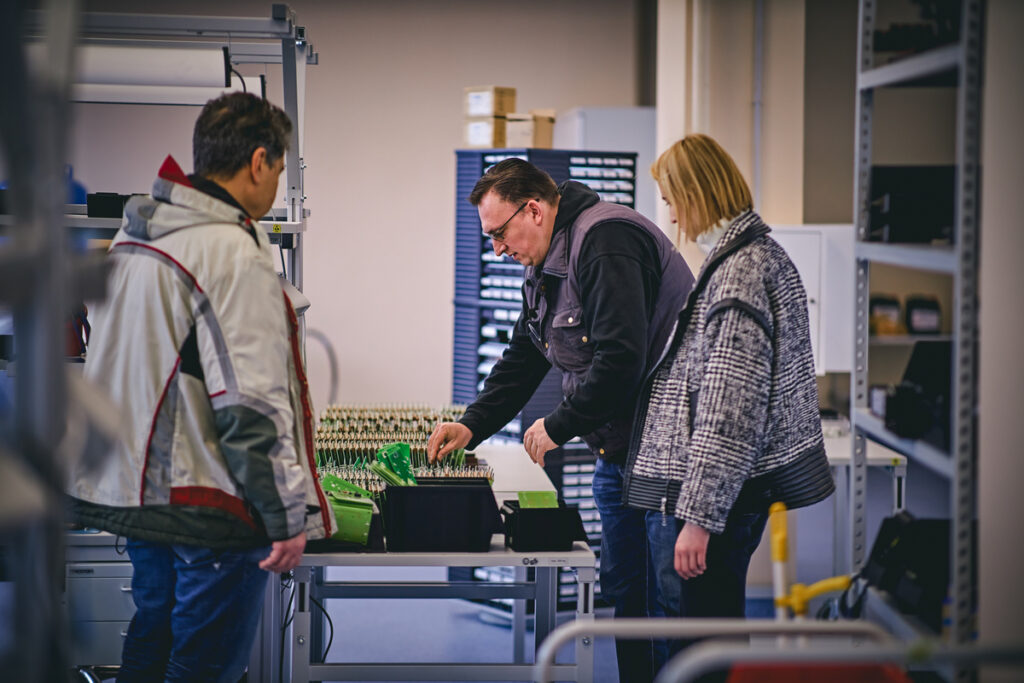
There are lots of reasons why SMDs invention has enhanced electronic components’ production. We highlight the main surface mount technology advantages and explain how they further influence the quality and efficiency of your developments.
- Space efficiency. SMDs have a much smaller footprint compared to their through-hole counterparts, allowing designers to pack more electronic manufacturing components into a limited space, making devices smaller and sleeker.
- Enhanced performance. The shorter lead lengths and reduced parasitic capacitance and inductance of surface mount devices enable higher operating frequencies and improved signal integrity.
- Automated manufacturing. SMD components are ideally suited for automated electronic assembly processes, leading to increased efficiency and reduced manufacturing costs.
- Weight reduction. The compact size of any SMD results in lighter electronic devices, making them more portable and convenient.
- Thermal performance. Surface mount devices have better thermal conductivity, enabling better heat dissipation, which is crucial for high-power applications.
- Efficient printed circuit board assembly. During the automatic installation process, SMDs are usually placed accurately and provide secure mounting.
- Excellent physical tolerance. Surface mount technology is excellent for operating at high frequencies due to connections with stable solder.
- Less expensive components. Finally, the application of surface mount technology means that you spend less money on SMDs than through-hole elements, which makes your factory more cost-effective.
How does surface mount technology work?
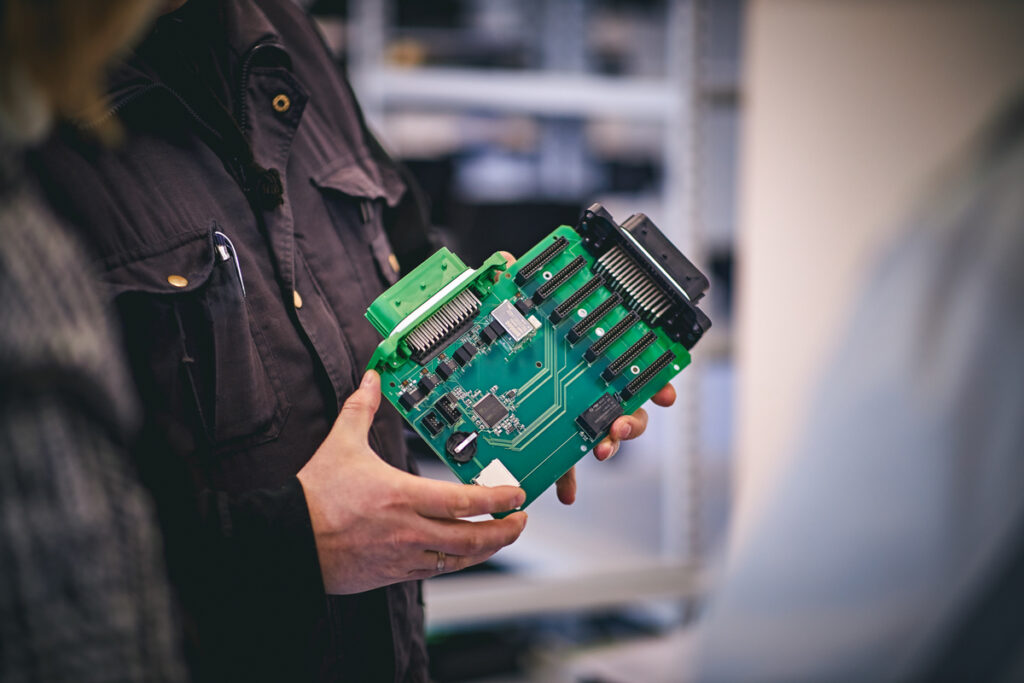
Surface mount technology (SMT) supports various components, including resistors, capacitors, integrated circuits, diodes, transistors, and many more. The fundamental principle of the process lies in electronic components’ miniaturization. This is achieved through the process described below.
- Stencil printing. A stencil, typically made of stainless steel, is aligned over the circuit board. Solder paste is then applied through the stencil onto the board’s designated pads, which act as soldering points for the SMT components.
- Component placement. Automated machines or pick-and-place robots precisely position SMT components onto the solder paste-coated pads. Vision systems on the machines ensure accurate alignment.
- Reflow soldering. The populated circuit board enters a reflow oven, where it undergoes controlled heating. The solder paste melts and bonds the SMT components firmly to the board. The oven’s temperature profile is critical, as it ensures that the components are soldered without damaging them.
- Inspection. After reflow soldering, the board is inspected with automated optical inspection systems. These surface mount technology equipment checks for misaligned components, solder defects, and other potential issues.
The Origins of Soldering Surface Mount Devices
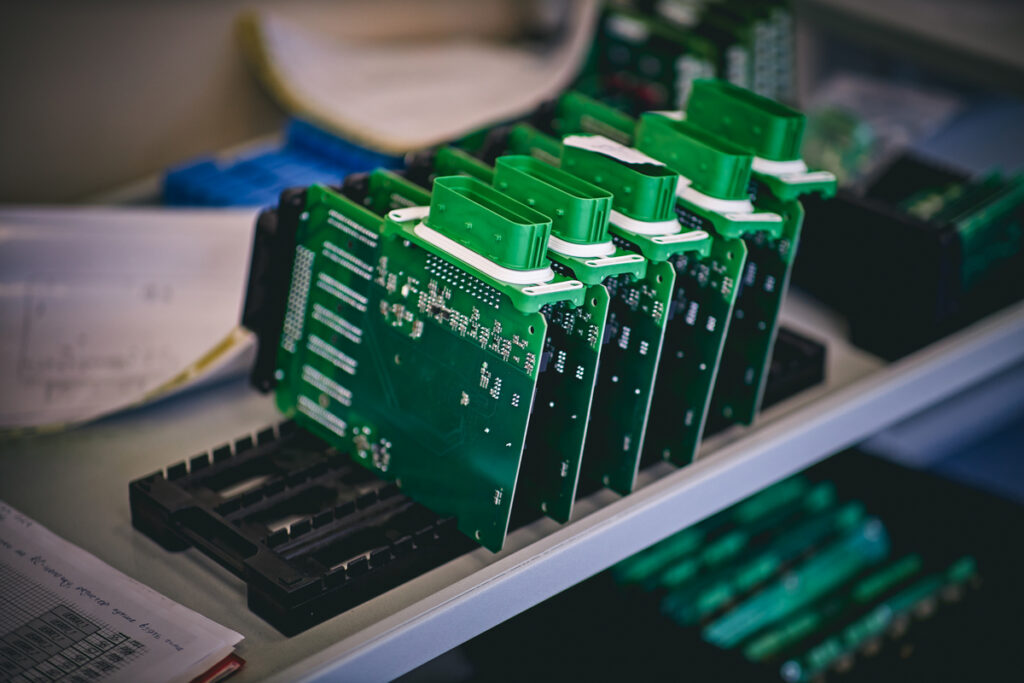
The true birth of surface mount technology is attributed to the 1960s, when innovative engineers and researchers began experimenting with mounting components directly onto the surface of printed circuit assemblies. The idea was to eliminate the need for drilling holes and inserting leads through them, thus significantly reducing the required board space.
During this period, various methods of soldering surface mount devices were explored. Initially, manual soldering techniques were used, which involved placing SMD components onto the circuit board and using handheld soldering irons to attach them. While this was a step forward, it proved to be time-consuming and less accurate for mass production.
As the demand for smaller, more powerful electronic devices grew, the need for efficient and precise manufacturing processes became evident. Automated surface mount assembly machines emerged in the late 1970s and early 1980s, marking a significant turning point in SMD manufacturing trends.
Pick-and-place machines, equipped with vision systems, were introduced to accurately position SMD components onto circuit boards. These machines increased production rates and significantly reduced manufacturing costs, making SMT a viable option for a wide range of electronic applications.
The final piece of the puzzle that solidified SMD’s success was the development of reflow soldering technology. After printed circuit board assemblies, they were subjected to a carefully controlled heating process, where the solder paste melted, forming solid and reliable solder joints. The introduction of reflow soldering in the mid-1980s allowed for the mass production of surface mount devices, ensuring consistent and high-quality solder connections.
Wrapping Up
The surface mount device technology is a game-changer in the electronics industry, enabling the production of compact, high-performance, and cost-efficient devices that have become integral to our modern lives. As this development continues to evolve, it promises to unlock even greater possibilities, driving innovation and pushing the boundaries of what is achievable in the electronics world.